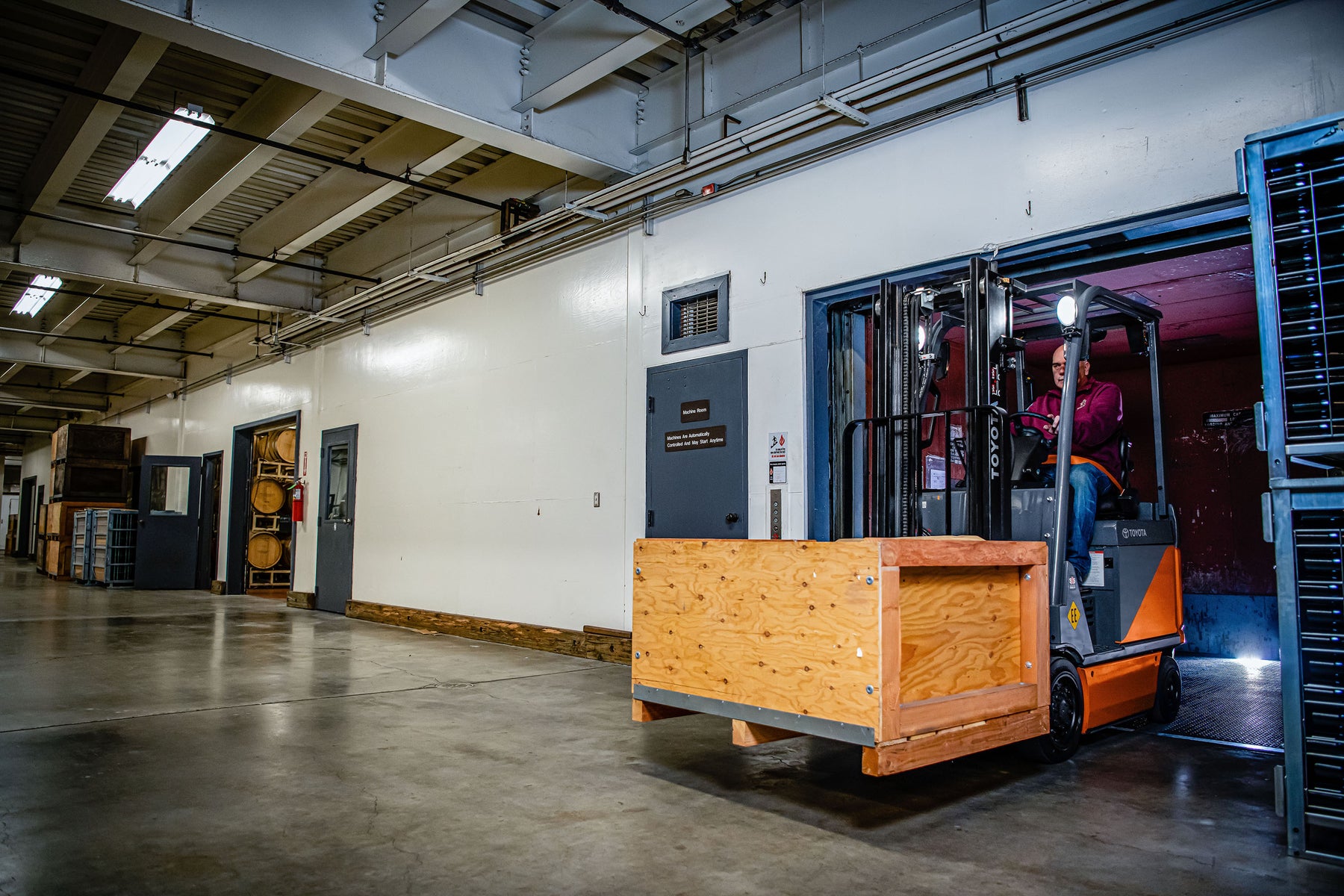
How to Evaluate Your Materials Handling Needs
If your growing business involves a materials handling component (warehousing, shipping, receiving, etc.), eventually your needs may outstrip the physically abilities of your employee teams. In the initial stages, loading, unloading and inventory rotation may involve nothing more than human power and a few dolly carts. But as your raw materials and stored products increase in size and scope, you may need lifting equipment that can move entire pallets rather than single items, or shift entire shelves of product from one area to another in a short time. You may need a forklift, and you may benefit by investing in more than one.
But how much lifting power can you afford? And how much do you need? If you overinvest, your expensive, underused machines will still need maintenance, attention and storage. If you underinvest, you’ll be stuck with a lift truck that can’t handle the necessary tasks—but nevertheless requires the same maintenance, attention and storage. So how can you find the right fit? What details should you factor into this calculation? Here are a few things to keep in mind.
Plan for the (near) future
As you estimate your growing needs, keep your estimation limited to the life span of your purchased or rented lift truck. How fast will your needs outgrow the limitations and specifications of your equipment? When will you need to make this decision again?
Consider your entire business cycle
You may need a large amount of assisted lifting power during your busiest season, but how long will this season last? And how will your needs drop when it ends? A summer business may rely heavily on a truck that sits in storage for the rest of the year. So, factor in depreciation and maintenance costs and consider renting a truck each year if these costs outweigh the benefits of a purchase.
Your people do some heavy lifting, but at what cost and risk?
Small tasks that can be accomplished by hand trucks and human labor may not require a forklift—until the day an employee becomes injured by a heavy load. Pushing this limit can lead to suffering for the employee and financial damage to the company, so invest long before this limit is reached.
Estimate the weight, bulk and dangers of an average load.
The manufacturing specifications of your truck will need to meet and exceed the weight, size and height of a standard load. But if your business is growing or changing, this number may change as well. Calculate for the future (the near future), not the present.
Factor workplace layout into the equation.
High shelves, narrow aisles and indoor/outdoor usage may affect your lifting needs. Research your chosen lift truck carefully to make sure it fits your workplace design and meets the needs of your employees.
Leave a comment